Precision Plastic Injection Molds
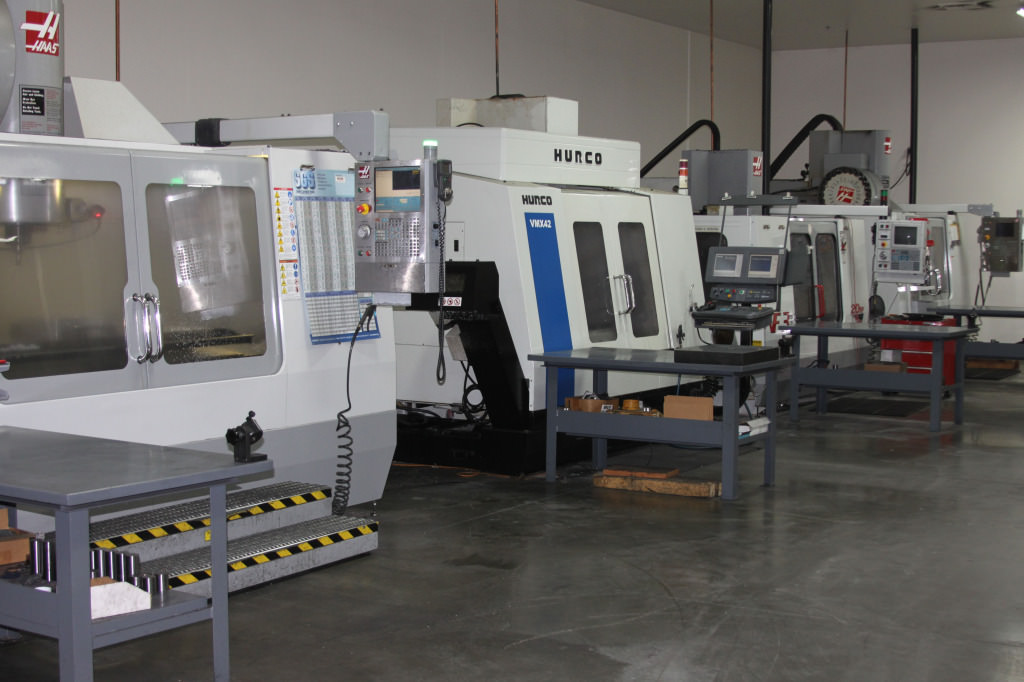
Cutting-Edge Technology Ensures Precision Plastic Injection Molds
PRe Plastics builds precision plastic injection molds for our customers, utilizing the advanced machining capabilities in our state-of-the-art toolroom. Our 4-axis CNC milling centers, traditional mills, and precision EDM machines place us at the forefront of custom injection molds in both aluminum and steel, depending on specifications. This range of machining methods indicates our philosophy on building molds, which is to build a precision tool in the quickest and most economical way possible. Our toolroom and production floor are under the same roof, facilitating the quick mold repairs by our expert toolmakers needed to keep production going. When overall lead time and costs are factors, we also offer MUD and Omni Mold frames and inserts.
Our comprehensive custom capabilities allow us to build the precision tooling needed for any project, including but not limited to:
- Challenging Multi-Cam Molds
- Hot Runner and Valve Gate Systems
- Overmolds
- Insert Molds
- 3-Plate Molds
- Family Molds
Mold designs are created in PTC Creo Expert Moldbase Extension®, complete with libraries of mold base and component suppliers worldwide. The final mold design is linked to the part design, so any modifications later made to the base part are automatically updated in the mold base and cavities in the mold design, which saves time and ensures dimensional accuracy.
Custom Solutions Built From Experience
PRe Plastics utilizes our extensive plastic manufacturing experience to help create custom solutions aimed at ensuring our customers’ products’ ultimate success. Based on the expected product life and chosen material, PRe Plastics may recommend an aluminum or class A steel tool to meet the project specifications. Aluminum molds, which are easier to machine, greatly reduce a tool’s lead time and cost. Additionally, improved heat transfer during processing in aluminum molds reduces part costs through faster cycle times. Class A steel molds, on the other hand, are beneficial for projects with a long life span due to their durability, precision, and ability to meet high cosmetic requirements. Another benefit of steel molds is their ability to run highly abrasive materials.
Comprehensive Mold Capabilities
Cycles | Uses | Investment | |
Class 101 Mold | 1 million or more | Extremely high production and fast cycle times | Class 101 molds are the highest priced and made with only the highest quality materials |
Class 102 Mold | Not exceeding 1 million | Good for parts with abrasive materials and/or tight tolerances | Class 102 molds are fairly high priced and made with materials of high quality |
Class 103 Mold | Not exceeding 500,000 | A very popular mold for low to medium production parts | Class 103 molds fall within common price ranges |
Class 104 Mold | Not exceeding 100,000 | Good for limited-production parts with non-abrasive materials | Class 104 molds fall within low to moderate price ranges |
Class 105 Mold | Not exceeding 500 | Prototype only | Class 105 molds are built inexpensively to produce a very limited number of product prototypes |
Your Full-Service Partner for Precision Plastic Injection Molds
PRe Plastics is your full-service partner for comprehensive plastic manufacturing and custom molds, from expert engineering to final assembly. Contact us today to learn more about our in-house tooling capabilities or request your quote to get started.